UW experts design masks for campus from scratch
Students and staff returning to the University of Wisconsin–Madison can protect each other from COVID-19 with masks designed by the university’s experts in textiles, filtration and infectious disease, and made by one of Wisconsin’s oldest companies.
By the time the fall semester begins, as many as 24,000 of the new face coverings will be available to help people comply with the campus requirement to wear masks in buildings and other situations in which distancing isn’t possible. Each one is the product of an exhaustive — and exhausting — process that wrestled with a feverish, worldwide rush on fabric inventories and ultimately churned through testing of 130 different combinations of materials to field a mask that textile chemist Majid Sarmadi calls “best in class.”
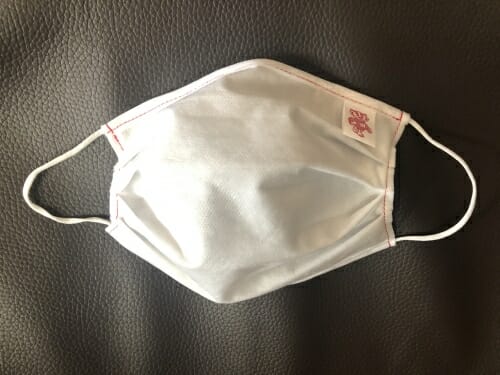
The mask, designed by UW–Madison experts in textiles, manufacturing and testing, will be available on campus in September. Courtesy of Peter Lukszys
Work began in March, when shortages of personal protective equipment required reserving stocks for particular users.
“We knew we had to prioritize medical-grade PPE for medical workers and for the UW researchers working on COVID-19, but we were determined to have a high-quality option for these others who were still on campus,” says Daniel Bornemann, University Housing access control and small projects manager.
Leaders from University Housing, UW Hospital and UW–Madison’s Environment, Health & Safety spurred the organization of a team of dozens, including Sarmadi, a School of Human Ecology professor with industry experience testing textile products, and David Rothamer, an engineering professor who reworked his combustion engine laboratory to measuring the filtering properties of prototype masks. Maria Kurutz, a SoHE design studies faculty associate, patterned and sewed scores of prototypes, even while teaching five classes in the spring semester. Peter Lukszys, a Wisconsin School of Business expert in supply chain management, drew up the group’s path from raw material to finished masks.
Steps typically laid out in sequence had to be undertaken simultaneously to meet a daunting schedule.
“Usually a new product introduction of this nature might take a year to 18 months from concept to mass production,” says Lukszys. “So, to design the product, iterate on multiple prototypes, and get it into production, we were moving at a much, much faster pace.”
To complicate matters, finished PPE wasn’t the only thing in short supply. Even in prototyping, the group was racing to get what they needed.
“There was a lot of not sleeping,” says Bornemann, relating a story of placing an order for a particular textile by phone one evening early in the process. “When I started giving (the customer service agent) my payment information, there were 15 rolls of the material to buy. Five minutes later, with all my info processed, there were just four.”
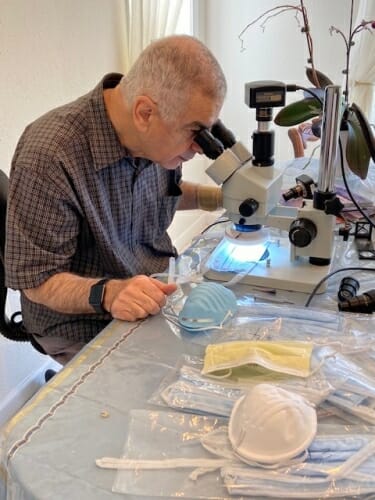
Textile chemist Majid Sarmadi examines sample masks while choosing material for a UW–Madison-designed face-covering. Courtesy of Majid Sarmadi
Making a mask that would be effective, easy to wear and durable meant managing a long list of sometimes competing considerations.
“Could it be woven fabric, even if they would ravel a bit after five washes? Could we get Badger Red thread in a timely fashion? Would it be more expensive?” Kurutz says. “These and other aesthetic and efficiency questions came into play, even as we were ultimately focused on having the highest filtration, breathability and comfort possible for the end user.”
Rothamer’s lab tested pairs of prototype masks until the group arrived at a design comprising three layers of spun-bond polypropylene material that can be hand-washed up to five times without significant effects on filtration. The mask’s filtration efficiency exceeds any other publicly available cloth mask the team has tested, while its cost (about $3 each) is comparable to many single-use masks.
BioForward Wisconsin helped Lukszys find the right match for scaling up the sewing operation: Brookfield-based Laacke & Joys. Workers at the 176-year-old manufacturer have made 7,000 of the masks — with another 12,000 on the way, bringing production thus far up to 24,000. UW–Madison units can now place their own orders through the university’s standard purchasing channels.
“I’m really very pleased with what the team developed in such a short time in terms of filtration and pressure drop (breathability),” Rothamer says. “It just goes to show — if you get the right group of people together with the right complementing expertise, you can move these things surprisingly fast to achieve a high-quality product.”
Not coincidentally, three of the units involved in the mask project — the schools of Human Ecology and Business and the College of Engineering — also helped launch UW–Madison’s new Design + Innovation master’s degree, which fosters students’ skills to address real-world problems.