TEAM Lab provides hands-on learning experience in modern machine shop facility
With countless tools and machines, the possibilities for bringing an idea to life are endless at the College of Engineering’s Technical Education and Manufacturing Lab.
Located in the Engineering Centers Building, the lab is open to students, faculty and staff affiliated with the college. For some, the lab has become a gateway for finding solutions and building projects to help others in the community.
Biomedical engineering student Sahand Eftekari worked with TEAM Lab in collaboration with three other students to make a product for a local Madison client: a prosthetic foot.
“We started with a problem and not really any idea of how to solve it, but we were able to walk our own way through and figure it out at TEAM Lab,” Eftekari said. “We wouldn’t have been able to do it without their help.”
Over the course of three semesters, Eftekari and his teammates built a prosthetic foot that would provide their client with the flexibility and range of motion to weight lift and remain active in his job with law enforcement.
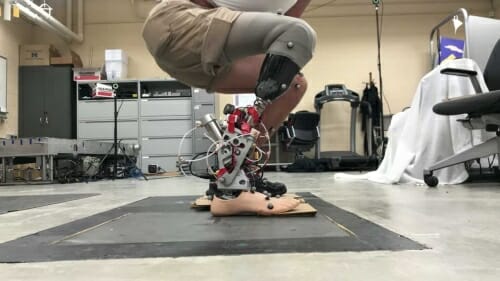
Eftekari and his teammates built a prosthetic foot in the TEAM Lab.
TEAM Lab serves as a resource to teach students machining, woodworking and welding, as well as how to safely use equipment found in a modern machine shop.
Not only does it provide students with hands-on experience in the creation of innovative projects, it shapes them into “more competent and well-rounded engineers,” says instrument maker Paul Kijak.
“We want to teach students how to use these pieces of equipment safely and then go out into the workforce as a better engineer,” Kijak said. “This experience rounds out an engineering education that goes beyond the classroom.”
Eftekari says his experience at the lab has enabled him to apply the skills he learns in the classroom to a real-world setting.
“Everything that I have learned at TEAM Lab is applicable and was useful in some way to the project,” he said. “You actually have to not only figure out how to solve a problem, but you have to design it and be confident enough for it to work — and for it to work every single time.”
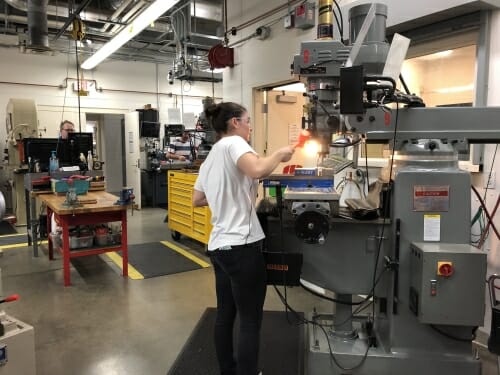
Students are trained in machining, woodworking, welding and equipment safety at TEAM Lab. Kayla Huynh
Upon completion of training, participants are granted permits which provide access to higher level machines and resources. The staff — which is comprised of professional instrument makers and trained students — are available to assist and guide those who are working in the facility.
Matt Michalak, a former lab staff member who now works at Phoenix, a local company that makes neutron generators, described the space as a “collaborative community” where students and staff can learn from each other and even from their mistakes.
“TEAM Lab has shown to a lot of students that you can modify existing ideas to make a product better and more efficient,” he said. “It’s a collaboration — students can bring an idea to TEAM Lab and work with others to make a better, quicker design that’s easier to make and functions better.”
The experience of building projects at TEAM Lab offers hands-on learning, something Michalak said is valuable to employers.
“Classes are oftentimes focused on theory or ideal situations, whereas in the lab, you’re dealing with the imperfections and the nuances that aren’t well-captured in equations or fundamental principles,” he said. “There’s a lot of magic and art that comes into the process.”